Understanding Fire Brick: The Essential Refractory Material for High-Temperature Environments
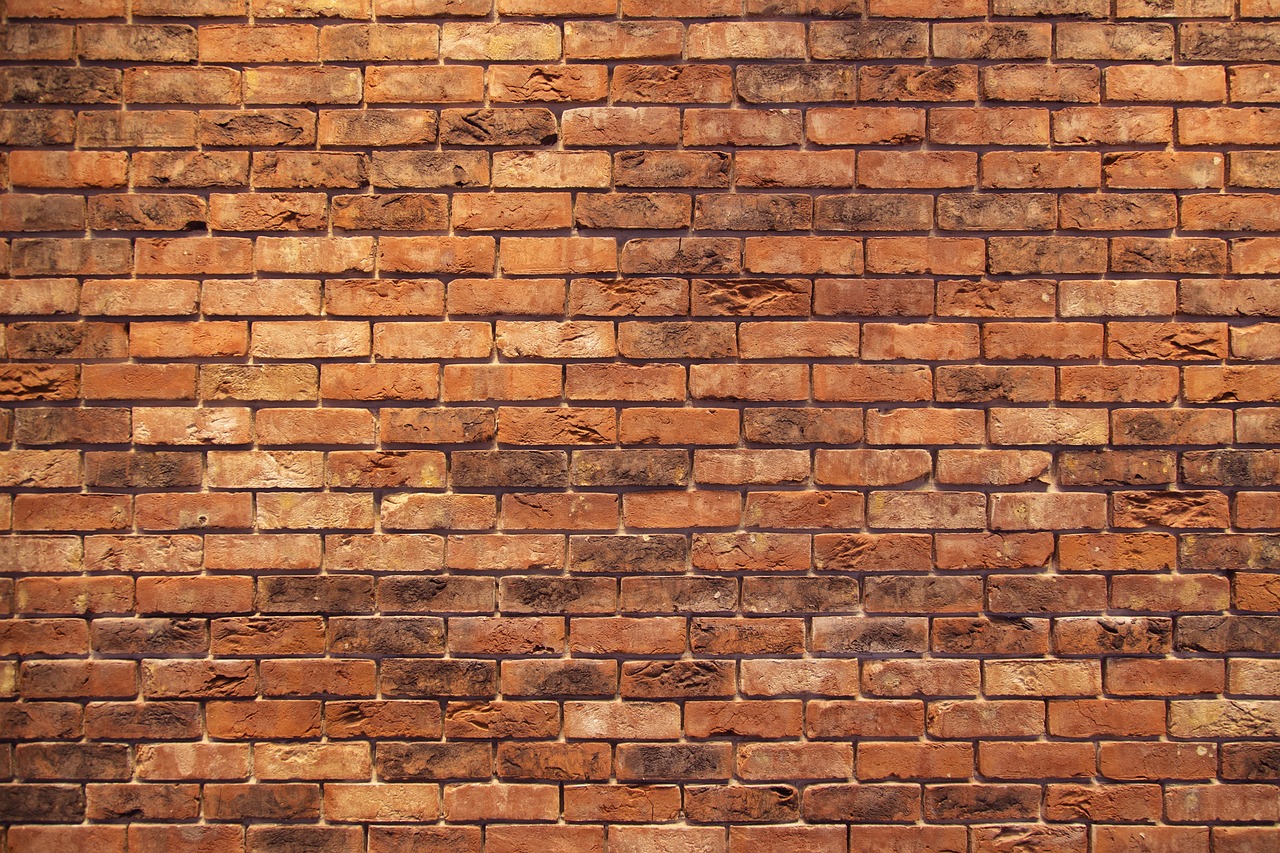
If you’ve ever wondered how industrial furnaces, fireplaces, or pizza ovens can withstand extreme temperatures without damage, the secret often lies in the use of fire brick. This specialized construction material is designed to endure intense heat, ensuring safety, efficiency, and longevity in various high-temperature applications. In this comprehensive guide, we will explore what fire brick is, its different types, material composition, properties, applications, and how to select and maintain the right brick for your needs.
What Is a Fire Brick?
Basic Description
At its core, a fire brick is a refractory ceramic material made to withstand high temperatures without losing structural integrity. Unlike regular clay bricks used in common construction, fire bricks are engineered with specific compositions and manufacturing processes to resist thermal shock, chemical attack, and physical wear. They are often characterized by a dense, heat-resistant structure that reflects and absorbs heat efficiently, making them indispensable in environments that demand high thermal performance.
Historical Context
The use of fire brick dates back to ancient civilizations like the Romans, who employed refractory bricks in their kilns and furnaces. Over centuries, advancements in material science led to improved formulations, allowing for more durable and efficient bricks. Today, modern fire brick technology evolves continuously, incorporating new materials and manufacturing techniques to meet the demanding needs of industries such as steel production, glass manufacturing, and even culinary arts like brick ovens and pizza stoves.
Types of Fire Bricks
Standard Fire Bricks
These are versatile, economy-grade bricks suitable for general high-temperature applications. They typically withstand temperatures up to 1,200°C (2,192°F) and are used in fireplaces, fire pits, and some industrial settings. Standard fire bricks are usually made from alumina or silica, providing basic thermal resistance.
Refractory Fire Bricks
Designed specifically for extreme environments, refractory fire bricks can endure temperatures exceeding 1,600°C (2,912°F). They are essential in high-temperature furnaces, kilns, and blacksmithing setups. Their composition includes high alumina or magnesia content, which ensures durability under intense heat and chemical conditions.
Insulating Fire Bricks
Unlike dense refractory bricks, insulating fire bricks prioritize low thermal conductivity over load-bearing strength. They are lightweight and used in applications where heat retention is critical, such as in oven linings or insulation layers in industrial furnaces. They typically withstand temperatures up to 1,200°C but excel at limiting heat transfer.
Acid-Resistant Fire Bricks
These bricks are formulated to resist corrosion and degradation caused by acids and chemicals encountered in industrial processes. They are ideal in chemical reactors, waste incinerators, and other environments where chemical attack is prevalent. Their composition often involves silica-based materials with specific additives.
Material Composition and Manufacturing
Common Materials
- Alumina (Al₂O₃): Provides high heat resistance and mechanical strength, especially in high-alumina refractory bricks.
- Silica (SiO₂): Used in traditional fire bricks, offering good thermal stability but less chemical resistance.
- Magnesia (MgO): Adds chemical resistance and is often used in bricks for steel manufacturing.
- Other Additives: Such as zirconia, chromite, or graphite, tailored for specific industrial needs.
Manufacturing Processes
The manufacturing of fire brick involves several critical steps:
- Shaping and molding the raw materials into desired forms, whether through extrusion, pressing, or casting.
- Drying the shaped bricks to remove moisture, preventing cracks during firing.
- Fire treatment at high temperatures, typically between 1,200°C to 1,600°C, to achieve the necessary hardness and thermal stability.
- Quality control measures, including mechanical testing and thermal analysis, ensure each batch meets industry standards.
Properties and Performance
Thermal Resistance
Fire bricks are capable of absorbing, reflecting, and insulating heat. Their low thermal conductivity makes them efficient in heat retention, which is vital in applications like fireplaces and kilns.
Mechanical Strength
These bricks must sustain load without cracking or spalling under thermal stress. High-density refractory bricks have excellent compressive strength to support furnaces or structural components.
Chemical Resistance
Properly formulated fire brick resists corrosion from chemicals, acids, and slags common in industrial processes, thereby extending their lifespan.
Durability and Lifespan
Factors influencing their longevity include exposure conditions, temperature cycles, and maintenance routines. Well-chosen fire brick can last several decades with proper care.
Applications of Fire Bricks
Fireplace and Stove Construction
Because of their aesthetic appeal and thermal properties, fire bricks are preferred for indoor fireplaces, wood-burning stoves, and outdoor fire pits, providing warmth and safety.
Industrial Furnaces and Kilns
In steel, ceramics, and glass industries, fire brick forms the lining of kilns and furnaces, ensuring the equipment withstands intense heat and abrasive conditions. For example, they are used in industry standards for refractory materials.
Boilers and Incinerators
Such structures require durable lining to prevent heat loss and protect the integrity of the equipment over time.
Outdoor Fireplaces and Pizza Ovens
Fire brick provides the heat-retaining properties needed for outdoor cooking appliances, ensuring even heating and long-lasting operation.
Chimney Linings and Fire Pits
Properly installed fire bricks prevent heat damage to surrounding structures and improve safety.
Advantages of Using Fire Brick
- High-temperature durability: Withstands extreme heat without degrading.
- Energy efficiency: Reflects heat back into the furnace or oven, reducing energy consumption.
- Safety benefits: Minimizes fire risk through high thermal stability.
- Longevity and low maintenance: Can last for decades if properly maintained.
Choosing the Right Fire Brick
Considerations
- Temperature requirements: Match the brick’s maximum temperature resistance with your application’s demands.
- Chemical environment: Use acid-resistant bricks in chemical or corrosive settings.
- Structural load: Ensure bricks have adequate mechanical strength for supporting structures.
Factors to Consider
- Cost and availability: Balanced with the quality needed for your project.
- Compatibility: Ensure the brick material aligns with existing structures for seamless integration.
- Sustainability: Consider eco-friendly options or manufacturers committed to environmentally responsible practices.
Installation and Maintenance Tips
- Proper installation practices: Use compatible mortar or refractory cement; maintain proper spacing and alignment.
- Regular inspection routines: Check for cracks, spalling, or signs of wear periodically.
- Repair and replacement guidelines: Replace damaged bricks promptly to prevent further deterioration and ensure safety.
Buying Guide
When purchasing fire brick, consider retailers specializing in refractory materials, such as industrial supply stores or online vendors. Look for certifications and industry standards compliance, such as ASTM or ISO ratings. Price points vary based on material quality, branding, and application specifics. Always check for the brick’s temperature rating, chemical resistance, and size compatibility to your project.
Common Problems and Troubleshooting
- Cracking and spalling: Often caused by thermal shock or improper installation. Solution: Use insulating bricks for thermal shock zones and ensure proper curing.
- Reduced thermal efficiency: Due to cracking or contamination. Solution: Regular cleaning and inspection.
- Signs of replacement needed: Cracks, significant spalling, or chemical degradation indicate that bricks should be replaced to maintain safety.
Future Trends and Innovations
- Advanced refractory materials: Nanomaterials and composites that offer better heat resistance and environmental friendliness.
- Eco-friendly manufacturing methods: Reducing emissions during production and using sustainable raw materials.
- Sustainable construction applications: Integration of fire brick technology in green building designs and energy-saving systems.
Summary Table: Properties and Applications of Fire Brick Types
Type of Fire Brick | Temperature Resistance | Density | Thermal Conductivity | Best Applications |
---|---|---|---|---|
Standard Fire Brick | Up to 1,200°C | Moderate | Moderate | Fireplaces, basic ovens |
Refractory Fire Brick | Exceeds 1,600°C | High | Low | Steel furnaces, kilns |
Insulating Fire Brick | Up to 1,200°C | Lightweight | Very Low | Oven linings, insulating layers |
Acid-Resistant Fire Brick | Variable, high in chemical resistance | High | Low | Chemical reactors, waste incinerators |
Questions & Answers (FAQ)
1. What is the difference between refractory and regular bricks?
Refractory bricks are specially formulated to withstand high temperatures and chemical attack, whereas regular bricks are intended for general construction and cannot tolerate extreme heat.
2. How long do fire bricks typically last?
With proper maintenance and application, fire brick can last several decades, often 20–50 years depending on usage and environment.
3. Can I install fire bricks myself?
Yes, with the right tools and knowledge, DIY enthusiasts can install fire brick. However, professional installation is recommended for complex or high-stakes projects.
4. Are fire bricks environmentally friendly?
Manufacturers are developing more eco-friendly refractory materials, but traditional fire brick production can produce emissions. Look for brands committed to sustainable practices.
5. What materials are best for outdoor fire pits?
Insulating or standard refractory fire bricks are suitable because they withstand outdoor conditions and high heat.
6. How do I know if my fire brick needs replacement?
Signs include cracks, spalling, excessive wear, or a noticeable decrease in thermal performance. Regular inspections can help determine when to replace.
7. Are there fire bricks suitable for chemical environments?
Yes, acid-resistant fire bricks are designed specifically for chemical exposure, ensuring longevity in such settings.
8. Can fire bricks improve energy efficiency?
Absolutely. Their reflective and insulative properties help conserve heat, reducing fuel costs and improving overall efficiency.
9. Where can I buy quality fire brick?
Specialized refractory suppliers and industry distributors, such as Refractory.com, offer a range of certified products suitable for various applications.
10. Are there environmentally friendly innovations in fire brick manufacturing?
Researchers are exploring biodegradable refractory materials and green production techniques to minimize environmental impact.
Understanding the various aspects of fire brick helps in selecting the right material for your specific needs—whether it’s for a cozy fireplace or a high-tech industrial furnace. Proper choice, installation, and maintenance extend the lifespan, enhance safety, and improve energy efficiency in your heat-related projects. For more detailed guides and suppliers, visiting industry-standard sites can provide further assistance.